When working with electrical products, understanding the different types of certifications is important for electricians to ensure we’re installing materials that have passed standardize testing procedures. Agencies like UL (Underwriters Laboratories), CSA (Canadian Standards Association), and ETL (Intertek) provide various certifications that signify different levels of compliance and application for material manufacturers. This article goes into the distinctions between these three agencies, their certifications, and how the listing process works, overall.
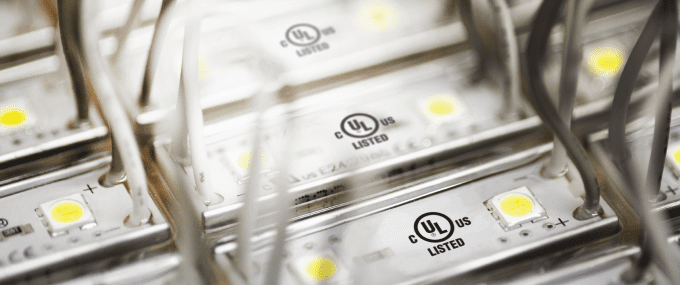
What are Product Listings?
Product listings certify that testing has confirmed a product meets the safety standards required for its intended use. These certifications are necessary because they ensure that products are safe, reliable, and perform as expected. Having some level of standardization, or “minimum standards” which everyone adheres to makes the industry as a whole produce quality products and quality installs. Listings are provided by recognized testing laboratories that evaluate products according to either national and international standards.
For electricians, and electrical inspecting bodies, ensuring products are listed is a requirement, in some cases, by the National Electrical Code. A few examples of codes mentioning products to be “listed” are:
2023 NEC 110.3(B) Installation and Use.
Equipment that is listed, labeled, or both, or identified for a use shall be installed and used in accordance with any instructions included in the listing, labeling, or identification.
2023 NEC 334.40(B) Devices of Insulating Material.
Self-contained switches, self-contained receptacles, and listed nonmetallic-sheathed cable interconnector devices of insulating material that are listed for use without a box shall be permitted to be used without boxes in exposed or concealed installations.
2023 NEC 410.6 Listing Required.
All luminaires, lampholders, and retrofit kits shall be listed.
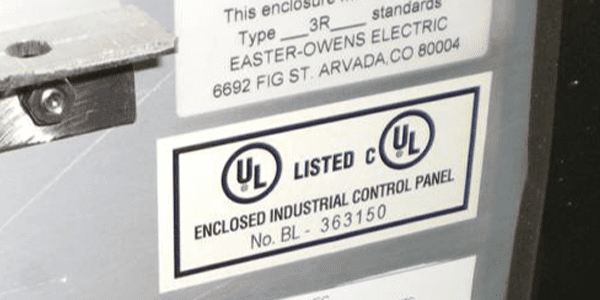
What if products aren’t listed?
Using non-listed products in installations can lead to significant safety risks, legal issues, and financial liabilities. Recognized agencies have tested and certified listed products, ensuring they meet strict safety standards. This process serves as quality assurance testing, ensuring products meet high standards and minimize risks of harm or catastrophe. Non-listed products have not undergone rigorous testing to ensure they can safely handle electrical loads and operating conditions.
This lack of testing increases the risk of:
- Electrical Fires: Poor quality or substandard components can overheat, leading to fires. This is especially critical for high-current devices such as circuit breakers and wiring.
- Equipment Failures: Non-listed products may fail prematurely, causing disruptions and potential hazards in electrical systems.
Not all products need a listing in every situation. However, in electrical systems and components, significant risks exist, so many products require a listing. A circuit breaker, essential for safety, must have a listing to ensure it performs its function reliably under certain circuit conditions. We’ve actually seen instances where breaker and panel manufacturers did not adhere to product evaluation standards in the past, and because of this we now take this process more seriously.
Federal Pacific Electric (FPE)
An example of a product that was not following listing standards, and was actually lying to the public stating they were, was Federal Pacific. Several decades ago Federal Pacific Electric (FPE) panels and circuit breakers became notorious for their high failure rates and fire hazards. Many FPE Stab-Lok breakers failed to trip during overcurrent conditions, leading to overheating and fires. Consequently, these panels were not consistently reliable and lacked the necessary certifications to guarantee safety. This company was printing “UL Listed” on their products, stating their products were UL listed, when in fact they were not.
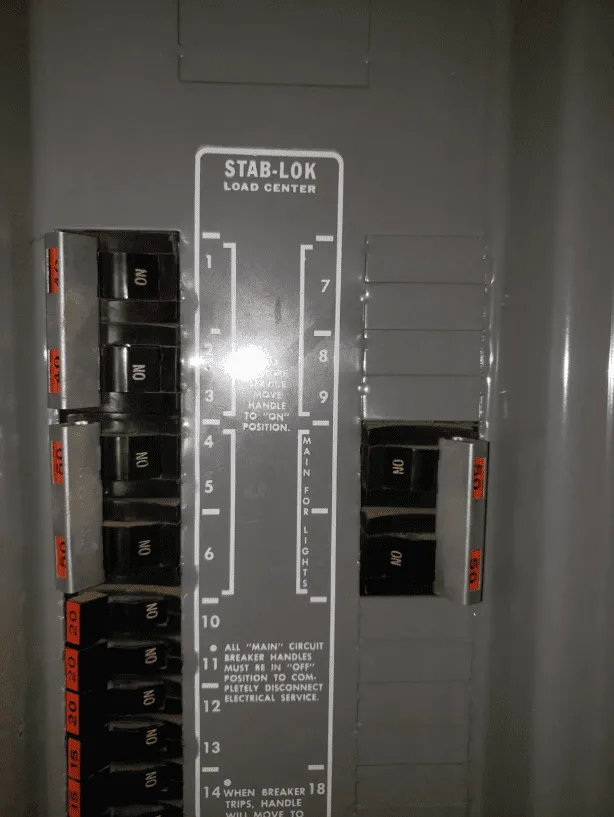
They continued to do this for decades, so much so that millions of homes built from the 1950s to the 1980s still have FPE panels installed in their homes across America. By the late 1970s, reports began to surface about FPE Stab-Lok breakers failing to trip during overcurrent conditions. A huge shift came when Consumer Reports published an article in 1980 highlighting the potential dangers of FPE breakers. The article raised awareness about the widespread nature of the problem and the need for further investigation.
In response to mounting concerns, the U.S. Consumer Product Safety Commission (CPSC) launched an investigation into FPE breakers in the early 1980s. The investigation aimed to determine whether these products posed a significant risk to consumers. Therefore the CPSC’s investigation revealed that many FPE Stab-Lok breakers failed to trip as intended, violating safety standards and increasing the risk of fire. Eventually, over time, Federal Pacific Electric Company ceased operations under that name and became involved in numerous class-action lawsuits for knowingly selling defective products with falsified listing information. This FPE fiasco underscores the importance of building and testing products to meet minimum standards, which listing agencies ensure.
Key Listing Agencies
UL is one of the most recognized independent testing organizations globally, however they’re not the only one. In fact, there are several listing agencies based in different countries that all work toward global standardization of product safety standards. Here in the U.S. and Canada there are three companies that carry the bulk of the weight for U.S. products: UL, CSA, and ETL.
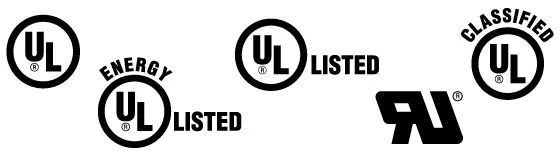
Underwriters Laboratories (UL)
UL tests and certifies products to ensure they meet specific safety standards. Products that pass UL’s testing criteria carry the UL mark, indicating compliance with stringent safety standards. A few of the most recognizable marks a UL tested product can carry are “UL Listed,” “UL Classified,” and “UL Recognized.”
UL Listed is one of the most comprehensive certifications provided by Underwriters Laboratories. It signifies that a complete product has undergone testing and meets UL’s safety standards.
- Scope: Applies to complete products intended for consumer or industrial use, such as appliances, electronics, and electrical components.
- Testing: Involves rigorous testing of the product’s performance, safety, and suitability for the intended use.
- Mark: Products that pass these tests are labeled with the UL Listed mark, indicating full compliance with UL standards.
- Examples: Circuit breakers, smoke detectors, electrical panels, and light fixtures.
UL Classified certification is typically used for products evaluated for specific properties, limited hazards, or suitability under specific conditions. It signifies that a product has undergone testing and meets UL’s standards for particular attributes or performance criteria.
- Scope: Applies to products tested for specific properties or performance under certain conditions, such as fire resistance, energy efficiency, or impact resistance.
- Testing: Focuses on evaluating the product for specific conditions, hazards, or performance attributes. The classification has a limit to the aspects for which the product underwent testing.
- Mark: These products carry the UL Classified mark, indicating compliance with the standards relevant to the specific tests or evaluations.
- Examples: Fire-resistant materials (e.g., fire doors, firestopping materials), HVAC equipment (e.g., components classified for energy efficiency or refrigerant safety), and building materials (e.g., insulation, roofing products classified for thermal resistance or impact resistance).
UL Recognized certification is typically for components rather than complete products. Therefore it signifies that a specific component has gone through necessary steps and meets safety standards for use within a larger system.
- Scope: Applies to components used within other products, such as power supplies, circuit boards, and other sub-assemblies.
- Testing: Focuses on the safety and performance of the component itself, often considering its integration into a larger system.
- Mark: These components carry the UL Recognized mark, often indicated by a backwards “UR.”
- Examples: Component-level transformers, capacitors, relays, and connectors.
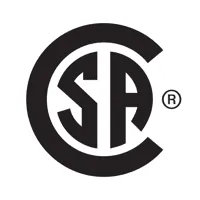
Canadian Standards Association (CSA)
CSA Group develops standards and provides testing, inspection, and certification services. Canada and the international communities widely recognize it. Products that meet CSA standards carry the CSA mark, signaling adherence to Canadian safety regulations.
- CSA Certified: Similar to UL Listed, this certification applies to complete products that have been tested for safety and compliance with CSA standards.
- CSA Component Acceptance: Analogous to UL Recognized, this certification applies to components tested for use within larger products.
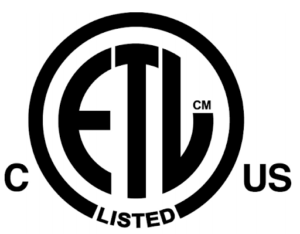
Intertek (ETL)
Originally known as Electrical Testing Laboratories, ETL is now part of Intertek, providing product testing, inspection, and certification services. Products that pass ETL’s evaluations carry the ETL mark.
- ETL Listed: Similar to UL listed, this certification indicates that a product has been tested and meets the safety standards. Products carry the ETL Listed mark.
- ETL Recognized Component: Similar to UL Recognized, this certification applies to components tested for safety and performance within larger products.
Listing Procedures
Once a product is manufactured, getting it listed involves a series of steps which are required to verify its compliance with relevant standards. There are two primary methods of getting a product tested and adhering to listing standards: submitting products to a testing agency for individual testing or setting up an in-house facility for ongoing testing and inspection.
1. Product Submission for Testing
- Initial Testing: The manufacturer submits a sample of the product to the listing agency, such as UL, CSA, or ETL for testing. This process includes:
- Design Evaluation: The agency reviews the product’s design to ensure it meets the relevant safety standards.
- Testing: The product undergoes various tests to check for electrical safety, fire hazards, mechanical stability, and other relevant factors.
- Certification: If the product passes all tests, it is certified and can carry the listing mark (UL, CSA, ETL).
- Follow-Up Services: To ensure ongoing compliance, the listing agency may conduct periodic follow-up inspections and testing.
2. Setting Up a Facility for Testing
For manufacturers producing large volumes of products or multiple product lines, setting up an in-house testing facility may be more efficient than having every variation of each new product and sku sent away for independent evaluation. To do this, however, there are procedures these large companies must adhere to:
- Facility Requirements: The manufacturer must set up a testing facility that meets the listing agency’s standards.
- Training and Certification: The agency provides training to the manufacturer’s personnel on testing procedures and standards.
- Regular Inspections: The listing agency conducts regular inspections of the facility to ensure compliance. These inspections verify that:
- Testing Procedures: The facility follows the correct testing procedures.
- Record Keeping: Maintaining accurate records of tests and results consistently.
- Product Consistency: Products continue to meet the standards required for listing.
Conclusion
Understanding product listings and the role of listing agencies like UL, CSA, and ETL is something electricians should consider. These certifications ensure that the products used in electrical installations are safe, reliable, and compliant with regulatory standards. Therefore, by adhering to the NEC requirements and utilizing listed products where required, electricians can enhance the safety and and quality of their work, protect themselves from liability, and build trust with their clients.